The Ultimate Guide to Kydex Vacuum Forming Membrane
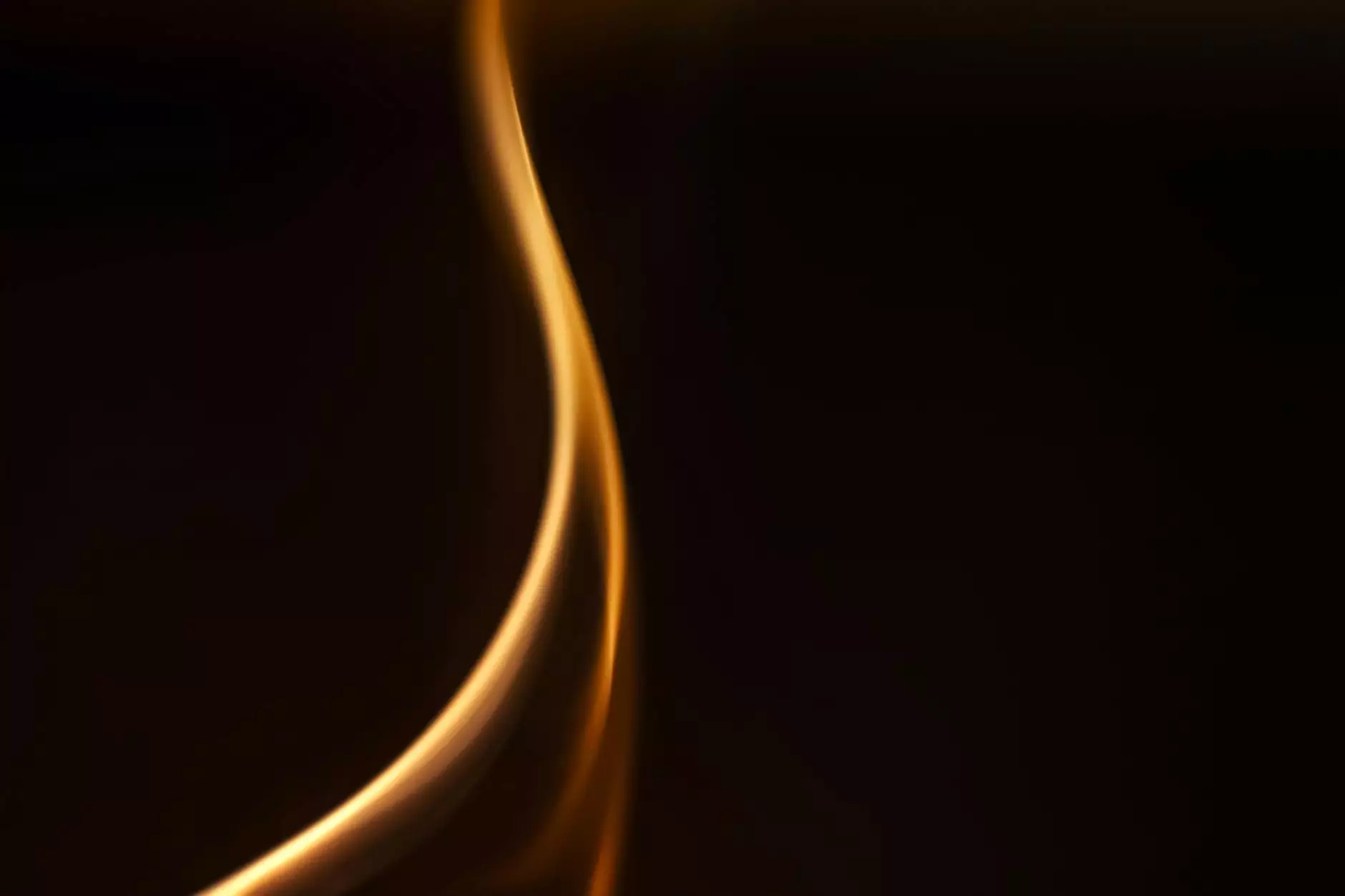
The kydex vacuum forming membrane is a revolutionary material that has transformed many industries, particularly in manufacturing and product development. This article delves deep into understanding what Kydex is, how vacuum forming works, and the significance of the vacuum forming membrane in various applications.
What is Kydex?
Kydex is a type of thermoplastic acrylic-polyvinyl chloride (PVC)-based material that is renowned for its versatility and durability. Developed in the 1960s, Kydex is employed widely due to its numerous benefits, including:
- High Impact Resistance: Kydex is resistant to scratches, dents, and impacts, making it an ideal choice for protective equipment.
- Ease of Fabrication: It can be easily formed and shaped, allowing for intricate designs.
- Color Variability: Kydex comes in a vast range of colors and finishes, catering to various aesthetic requirements.
- Lightweight: The lightweight nature of Kydex makes it a favored choice in applications where weight is a concern.
Understanding Vacuum Forming
Vacuum forming is a manufacturing process that involves heating a plastic sheet, then stretching it over a mold and applying vacuum to form it into shape. This process is particularly effective for Kydex materials due to their thermal characteristics. Here’s a step-by-step breakdown of how vacuum forming works:
- Heating: The Kydex sheet is heated until it reaches a pliable state.
- Forming: Once malleable, the sheet is immediately placed over a mold.
- Vacuum Application: A vacuum is applied to suck the sheet into the mold, ensuring that every detail of the mold is captured.
- Cooling: The formed Kydex is then cooled to retain its new shape.
The Importance of Kydex Vacuum Forming Membrane
The kydex vacuum forming membrane is critical in ensuring the effectiveness of the vacuum forming process. This membrane acts as a barrier that helps maintain the vacuum's integrity during the forming process. Its role includes:
- Facilitating Perfect Shape Capture: The membrane ensures that Kydex can conform seamlessly to the mold, producing precise and accurate products.
- Improving Turnaround Time: High-quality membranes speed up the vacuum forming process, leading to increased production efficiency.
- Enhancing Product Quality: A good vacuum forming membrane minimizes imperfections like bubbles or wrinkles, resulting in a superior finish.
Applications of Kydex Vacuum Forming Membranes
The versatility of kydex vacuum forming membranes allows them to be used across various industries. Here are numerous applications:
1. Industrial Applications
In industries such as automotive and aerospace, Kydex is used to create durable and lightweight components that withstand harsh conditions.
2. Medical Equipment
Kydex vacuum forming is essential in producing medical trays and cases that require stringent sterilization processes. The material's built-in properties make it suitable for such applications.
3. Consumer Products
Kydex vacuum forming allows for the production of various consumer goods, from custom toolboxes to phone cases, helping brands create unique and tailored offerings.
4. Environmental Solutions
Using Kydex in recycling processes demonstrates a commitment to sustainability, as this thermoplastic can be reformed and reused to minimize waste.
Why Choose Kydex Vacuum Forming Membrane for Your Business?
Businesses that incorporate kydex vacuum forming membranes into their production processes not only enhance their operational efficiencies but also achieve better product outcomes. Here are several reasons why choosing Kydex is beneficial:
- Cost-Effective: The durability and longevity of Kydex products reduce long-term costs associated with maintenance and replacements.
- Brand Differentiation: Customization capabilities allow businesses to stand out in competitive markets by offering unique and innovative solutions.
- Technical Support: Suppliers often provide extensive technical support, ensuring that businesses can optimize their processes effectively.
- Scalability: Kydex products are easily scalable, making them suitable for both small-scale and large-scale manufacturing.
How to Optimize the Use of Kydex Vacuum Forming Membrane
To maximize the benefits of kydex vacuum forming membranes, it's essential to implement best practices:
1. Material Selection
Ensure you're using the right grade of Kydex that matches your specific application. Different grades offer varying properties such as color, translucency, and strength.
2. Temperature Control
Maintain precise temperature control during the heating phase to achieve optimal forming conditions. Overheating can lead to deformation, while underheating can cause inadequate forming.
3. Mold Maintenance
Regularly inspect and maintain molds to avoid defects in products. Smooth and clean molds provide better impressions and ultimately enhance the quality of the finished product.
4. Quality Assurance
Implement a rigorous quality control process to check for defects in the created products, ensuring that they meet customer expectations and comply with any industry standards.
Conclusion: Embrace the Potential of Kydex Vacuum Forming Membrane
The kydex vacuum forming membrane is not merely a material; it's a gateway to innovation and efficiency in various industries. Businesses that adopt Kydex for their vacuum forming needs can expect to improve product quality, reduce production times, and enhance profitability. By understanding the benefits and applications of Kydex and following best practices for its use, companies can position themselves at the forefront of their industries.
For more information on Kydex vacuum forming and how it can benefit your business, visit us at vacuum-presses.com.