CNC Precision Machining: A Definitive Guide to Metal Fabrication
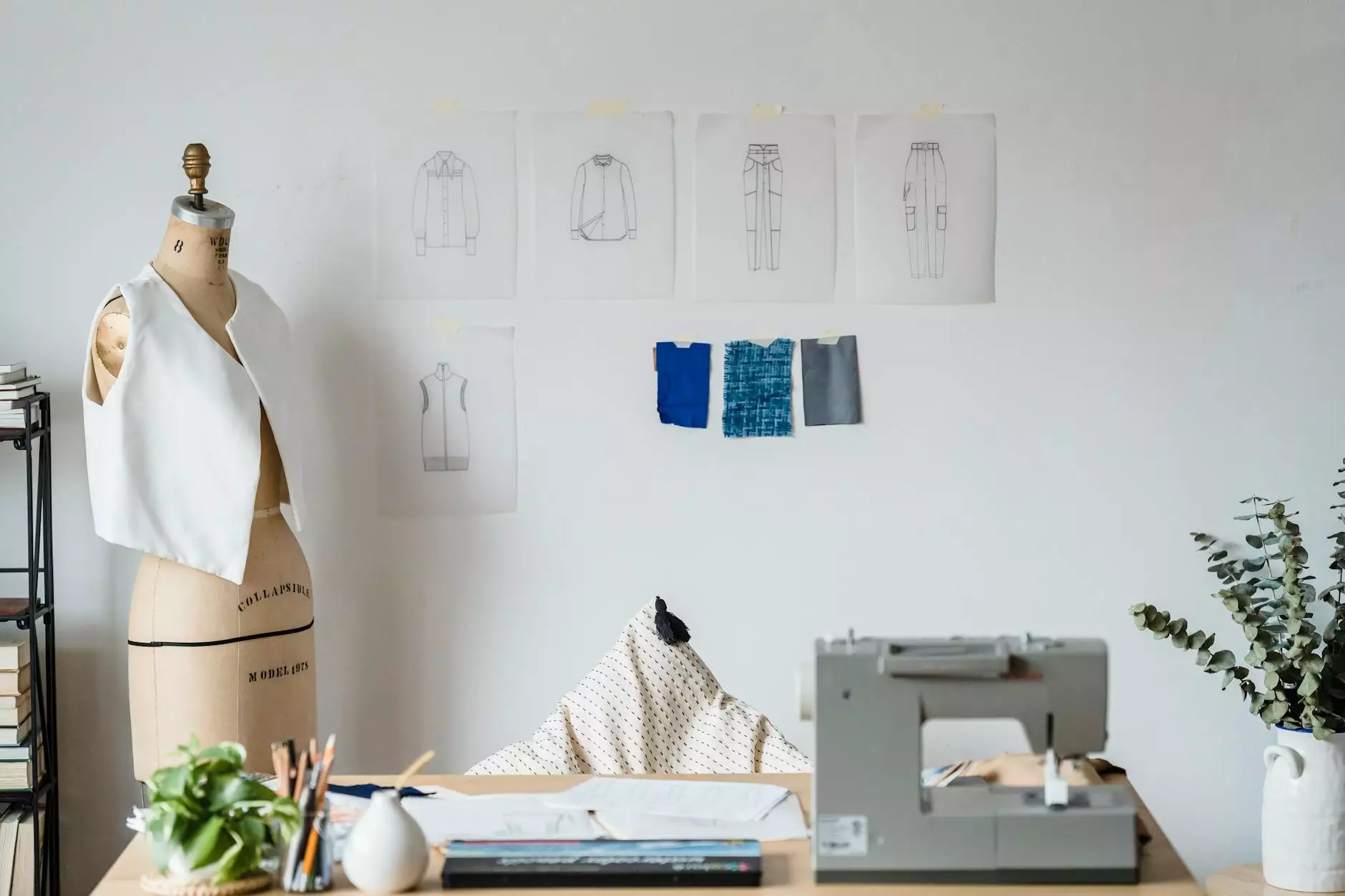
CNC precision machining has revolutionized the manufacturing landscape, offering unparalleled precision, efficiency, and versatility in the metal fabrication industry. With advancements in technology and the increasing demand for high-quality components, understanding the dynamics of CNC machining has become essential for businesses seeking to stay competitive in a rapidly evolving market. This article provides a comprehensive overview of CNC precision machining, its benefits, applications, and much more.
What is CNC Precision Machining?
CNC, or Computer Numerical Control, refers to the automation of machine tools through the use of computers executing pre-programmed sequences of machine control commands. Precision machining involves the removal of material from a workpiece to achieve desired dimensions and surface finishes. Together, these technologies enable the production of intricate parts with highly accurate specifications.
The Process of CNC Precision Machining
The process of CNC precision machining involves several key steps:
- Design Creation: Using CAD (Computer-Aided Design) software, engineers design the parts with exact specifications.
- Tool Path Generation: The CAD model is converted into a CNC program using CAM (Computer-Aided Manufacturing) software, which outlines the cutting paths for the machine.
- Machine Setup: The CNC machine is equipped with the necessary tools, and the workpiece is securely positioned.
- Machining: The CNC machine executes the programmed instructions, cutting and shaping the material to create the desired part.
- Quality Assurance: Finished products undergo rigorous inspection using precision measuring tools to ensure compliance with specifications.
Advantages of CNC Precision Machining
CNC precision machining offers numerous advantages over traditional machining methods:
- High Precision and Accuracy: CNC machines can produce parts to extremely tight tolerances, often within a few microns. This ensures the final product meets exact specifications.
- Consistency: Once programmed, CNC machines can reproduce parts consistently, significantly reducing variability and human error in the production process.
- Efficiency: CNC machines can run continuously with minimal supervision, leading to faster production times and lower labor costs.
- Complexity: CNC machining can create intricate designs that would be difficult or impossible to achieve with manual methods.
- Material Versatility: CNC precision machining can be applied to a variety of materials, including metals, plastics, and composites.
Applications of CNC Precision Machining
CNC precision machining is employed across various industries, delivering critical components for a wide array of applications:
Aerospace Industry
In the aerospace sector, CNC precision machining is essential for manufacturing components that require exceptional accuracy and reliability, such as turbine housings, brackets, and landing gear parts.
Automotive Industry
Automotive manufacturers utilize CNC machining for producing intricate engine parts, transmission housings, and custom accessories that enhance vehicle performance.
Medical Devices
The medical field demands high-quality, sterile components. CNC precision machining ensures the production of surgical instruments, implants, and devices that meet stringent industry standards.
Electronics
In electronic device manufacturing, CNC machining creates enclosures, mountings, and intricate circuit board components with high precision.
The Future of CNC Precision Machining
The future of CNC precision machining looks promising, with several trends likely to shape the industry:
- Integration with Advanced Technologies: The incorporation of AI, IoT (Internet of Things), and big data analytics into CNC machining will facilitate monitoring, predictive maintenance, and enhanced operational efficiency.
- Increased Automation: Automating more aspects of the machining process will reduce labor costs and improve consistency and output quality.
- 3D Printing Synergy: Combining CNC machining with additive manufacturing will create new opportunities for complex and lightweight structures, improving overall performance.
- Sustainability Practices: The industry is expected to adopt practices that minimize waste and enhance energy efficiency, aligning with global sustainability goals.
Choosing the Right CNC Precision Machining Partner
For manufacturers, selecting the right CNC machining partner is a crucial decision. Consider the following when evaluating potential partners:
- Experience and Expertise: Look for companies with a track record of success and experience in your specific industry. Expertise in CNC machining techniques and understanding of the materials is essential.
- Quality Assurance: Ensure the partner has robust quality control processes in place, including certifications like ISO 9001 and industry-specific standards.
- Technology and Equipment: Verify that the partner utilizes state-of-the-art CNC equipment and software that can handle your project requirements efficiently.
- Customer Service: A responsive and knowledgeable customer service team can significantly enhance collaboration and problem-solving capabilities.
Conclusion
CNC precision machining is more than just a manufacturing process; it’s a cornerstone of modern industry, driving innovation and efficiency. As businesses seek to improve their operations and product quality, understanding the benefits, applications, and future trends of CNC machining will be crucial. By choosing the right CNC machining partner, companies can optimize their production capabilities, ensuring they remain competitive in an increasingly complex market.
For more information on how CNC precision machining can enhance your business, visit deepmould.net today!