Understanding the Importance of Pressure Die Casting Manufacturers in Metal Fabrication
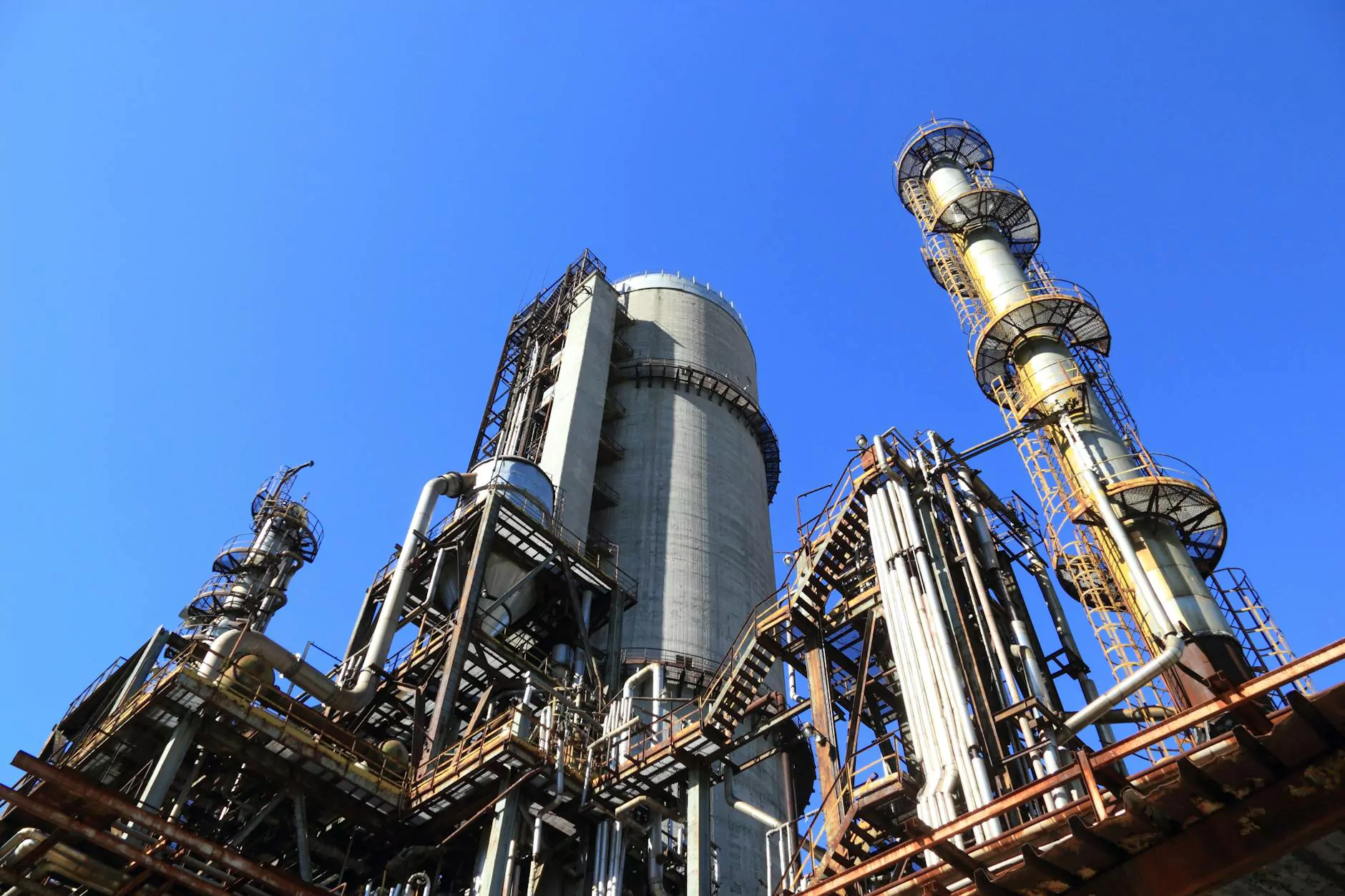
In the realm of modern manufacturing, the significance of pressure die casting manufacturers cannot be overstated. This specialized sector plays a crucial role in providing high-quality metal components for various industries, including automotive, aerospace, electronics, and consumer goods. This article delves into the intricate world of pressure die casting, examining its processes, benefits, and the leading manufacturers that drive innovation in this field.
The Basics of Pressure Die Casting
Pressure die casting, also known as high-pressure die casting, is a metal casting process that involves forcing molten metal into a mold cavity under high pressure. This technique is widely appreciated for its ability to produce intricate shapes with tight tolerances, making it ideal for mass production.
Key Components of the Pressure Die Casting Process
To fully understand how pressure die casting works, it's crucial to break down the process into its key components:
- Melting Furnace: The process begins with the melting of metal, which is usually aluminum, zinc, or magnesium, in a furnace.
- Injection Mechanism: Once the metal reaches the desired temperature, it is injected into a steel mold at high pressure, ensuring that it completely fills the cavity.
- Mold Design: The mold, made of durable steel, is intricately designed to match the specifications of the desired component.
- Cooling Phase: After the metal fills the mold, it is allowed to cool and solidify, forming the final product.
- Extraction and Finishing: Once cooled, the mold opens, and the newly formed part is ejected and may undergo additional finishing processes.
Advantages of Pressure Die Casting
The popularity of pressure die casting manufacturing is largely due to the numerous advantages it offers:
1. High Precision and Quality
The ability to produce components with precise dimensions and smooth surfaces is one of the significant advantages of pressure die casting. This precision reduces the need for extensive machining, which in turn lowers production costs.
2. Rapid Production Rates
With the capability for mass production, pressure die casting manufacturers can deliver a high volume of parts in a short time. This speed is especially beneficial in industries where time-to-market is critical.
3. Material Efficiency
The die casting process minimizes waste, making it a more eco-friendly option compared to traditional metalworking methods, where excess material is often discarded.
4. Versatility
Pressure die casting is suitable for various metals and alloys, making it an adaptable option for manufacturers looking to create diverse product lines.
5. Enhanced Mechanical Properties
Components produced through pressure die casting often exhibit superior mechanical properties, including greater strength and durability compared to those made from other manufacturing processes.
The Role of Pressure Die Casting Manufacturers
Pressure die casting manufacturers are the backbone of this industry, providing the expertise, technology, and resources needed to create high-quality components. Let's explore the essential roles played by these manufacturers:
1. Design and Engineering Support
Leading manufacturers, such as DeepMould, offer design assistance to clients, ensuring that the components are engineered for manufacturability and optimized for performance. This includes considerations for material selection, geometry, and production techniques.
2. Advanced Technology Integration
Investing in state-of-the-art technology is paramount for pressure die casting manufacturers. This includes utilizing computer-aided design (CAD) and computer-aided manufacturing (CAM) systems, as well as robotic automation to enhance efficiency and precision.
3. Quality Assurance and Testing
To maintain high standards, manufacturers implement rigorous quality assurance processes. This often includes non-destructive testing, dimensional inspections, and material property evaluations to ensure that each product meets industry standards.
4. Customization Capabilities
The ability to customize components based on specific client requirements sets top manufacturers apart. This flexibility allows for tailored solutions that can meet unique industry demands.
Challenges Faced by Pressure Die Casting Manufacturers
While the advantages are significant, pressure die casting manufacturers also face their share of challenges:
1. Cost of Equipment and Maintenance
High initial investments in specialized equipment and ongoing maintenance costs can pose financial challenges, especially for smaller manufacturers. However, these costs are often justified by the long-term benefits and return on investment through increased production efficiency.
2. Environmental Regulations
As global demand for sustainable manufacturing increases, die casting manufacturers must navigate complex environmental regulations. Implementing eco-friendly practices and reducing carbon footprints will be essential for compliance and market competitiveness.
3. Skill Shortages
The manufacturing industry faces a skills gap, with many manufacturers struggling to find qualified technicians who can operate advanced machinery and manage sophisticated processes.
Future Trends in Pressure Die Casting Manufacturing
The future of pressure die casting is bright, with several emerging trends shaping the industry:
1. Technological Advancements
Continuous advancements in technology, including the use of 3D printing for mold-making and integration of artificial intelligence in manufacturing processes, will drive efficiency and innovation in the field.
2. Sustainable Practices
Manufacturers are increasingly focusing on sustainability by optimizing energy consumption, recycling materials, and minimizing waste in production processes.
3. Increasing Demand for Lightweight Materials
With the automotive and aerospace industries pushing for lighter components to improve fuel efficiency, pressure die casting manufacturers are likely to explore new materials and processes to meet these demands.
Conclusion: The Vital Role of Pressure Die Casting Manufacturers
In conclusion, the importance of pressure die casting manufacturers in the metal fabrication landscape cannot be overlooked. Their expertise in producing high-quality components efficiently positions them as key players in various industries. As technology evolves, these manufacturers must adapt to meet new challenges and leverage emerging opportunities to remain competitive. Companies like DeepMould are at the forefront, exemplifying the commitment to quality, innovation, and customer satisfaction in the pressure die casting sector.
Embracing the future of manufacturing, pressure die casting will continue to play a pivotal role in shaping a more efficient and sustainable industrial landscape.